Engineers of ‘SPbU Dynamics’ have presented a robot capable of finding the smallest defects in pipes and accurately evaluating their parameters.
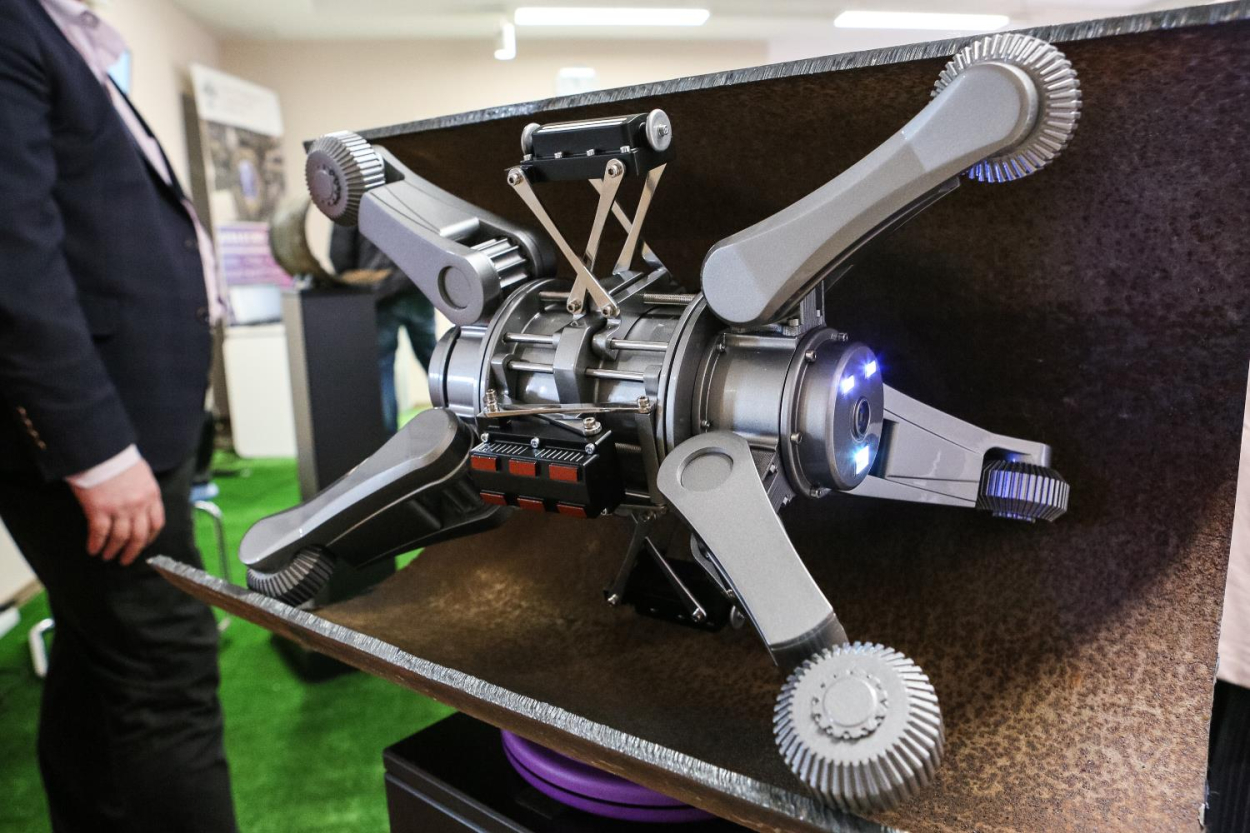
The development engineers of ‘SPbU Dynamics’ have demonstrated a unique pipeline inspection robot for diagnostics of both cold- and hot-water supply pipes as well as heating mains.
While moving inside the pipe, the innovative robotic diagnostic complex (RDC) is able to determine, with high accuracy, the location of the defect, its area and the thickness of the corroded pipeline wall.
Dmitry Grokholsky, the General Director of ‘SPbU Dynamics’, demonstrated a half-scale 3D-printed model of the robot. He showed how the device is inserted into the pipe and how it moves inside it.
‘The task is to provide accurate information about the condition of the pipe wall throughout its length, in each of its segments. A mobile laboratory goes to the site, where the robot is placed inside the pipe through a special tie-in. Then the device is remotely guided by the operator. The robot is equipped with a camera and machine vision, which is mission-critical,’ explained Dmitry Grokholsky.
The robot takes measurements which enable the location and area of the defect to be determined. The pipe wall thickness can also be evaluated beneath a layer of rust with 0.25 mm accuracy. The essential characteristics of the robot include: its ability to obtain measurements by sensors that work on various physical principles; and its complex kinematics. This is what distinguishes the RDC from other existing pipeline diagnostic tools on the market. Measurement accuracy is ensured by the sensors’ position stabilisation system designed to maintain a constant minimum gap between the pipe wall and the sensor surface. ‘A complex system of sensors placed on each leg of the robot enables a constant distance to be kept from the inspected surface. This ensures the high flexibility and mobility of the device,’ said Dmitry Grokholsky.
Another distinctive characteristic of the robot is its ability to withstand high temperatures. This gives the RDC advantages over other existing models, as it is designed to work in hot-water supply pipes and heating mains.
+80°C
This is the temperature which the ‘SPbU Dynamics’ invention is able to withstand. By contrast, analogous devices usually do not operate at temperatures exceeding +45°C.
The RDC has a unique system of stabilising its position relative to the pipe axis. This allows the robot to successfully by-pass various obstacles such as pipeline construction elements as well as foreign objects. The robot’s legs are adaptive to the pipeline bends. This enables the robot to navigate the most difficult pipe segments. The robot is able to inspect 70 metres of pipeline per hour; and it can analyse up to 700 metres of its internal surface in one go.
The development engineers' future plans include the creation of defect detection robots for the oil and gas industry.
Additionally, the device is equipped with an intelligent control system, which means it can work autonomously during a given time period. The development engineers noted that the robot is designed for inspecting main pipelines of 0.5 m diameter or larger. ‘At the moment we are developing software that will enable us to prioritise the inspection of certain segments. Thus, various factors are to be considered, including: thermal imaging data; the pipeline working lifetime; and the importance of a particular pipe segment to the city,’ emphasised Dmitry Grokholsky.